Hello.
Two years ago, 755 days to be exact, we shared how SEKISUI KYDEX was prepared to keep your business moving forward, while also keeping the safety of our employees as our top priority as the uncertainties of the COVID-19 pandemic began. Following that day, like many of you, we developed new processes, adapted to new ways (and places) of working, and implemented an ever-changing amount of safety protocols. While the pandemic is certainly not over, we do find it important to take a moment to stop and say – “We survived, and we are ready to begin thriving.”
Just as it was back then, the cornerstone of our successes are the extraordinary people that work at SEKISUI KYDEX. Through supply chain challenges like material shortages and price increases, our people stayed on top of the changing environment. The result of their passion, planning, and performance of our supply chain and manufacturing teams, is the delivery of our continued promise of on time shipping to keep your business moving forward.
For the past 24 months, the lead times and on-time performance of our Bloomsburg, PA campuses, manufacturing KYDEX® Thermoplastics, were consistent at a rate of 99% on time delivery.
This did not come easy, as we traversed many of the same challenges as our partners and competitors. Our teams experienced increased transitions, disruptions, medical material expedites, and ever-changing forecasts. Ultimately it was our Quick Response Manufacturing model, relationships with key suppliers, and our teams’ embracing challenges that allowed us to avoid a force majeure and keep customer delivery dates as the focus.
The supply chain team kept in constant contact with our suppliers developing contingency plans for changes to the raw material prices and availability. They collaborated closely with the business development team to understand the upcoming forecasts to ensure material was available for important programs like the CAE Air1 Ventilators for our customer Plastique Art (full story here). They also helped to develop new supply chains as we developed our first parts for the FORD and GE Healthcare ventilator program (full story here). Their diligence paid off.
"We have been navigating through many challenges in the world of Supply Chain. From price increases to shortages (raw material and transport) we have seen it all. We viewed these challenges as opportunities to grow and develop new skills, improve processes, and build stronger relationships with our vendors. As a result, we effectively served our customers with an outstanding on-time shipping performance. The achievement of 99% on-time shipping would not have been possible without the amazing people on our production floor or the support of our customers." – Max Good, Sr. Supply Chain Specialist
With material and orders in hand, the production scheduling teams were adjusting order schedules to accommodate the expedited orders. Over the past two years, our teams facilitated expedites for an average of % of all orders each month.
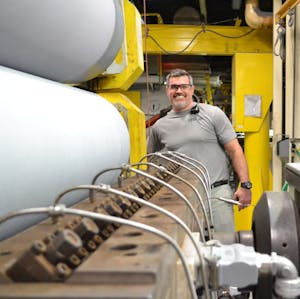
Bill Kitchen ensuring Quality material is running through the line.
The true grit behind our on-time shipments came from our manufacturing teams. They were flexible to work through the COVID-19 restrictions, wearing masks, social distancing and covering if a fellow coworker was out sick. They enhanced their abilities to change tooling quickly to meet the customer ship dates. Their dedication and hard work kept thermoplastics coming off the line and out the door.
They did all of this while working with the engineering and automation teams to gain efficiency through automation and technology changes on the production lines. The maintenance teams collaborated to keep current equipment running smoothly by making sure we had spare parts on hand and those changes and repairs were made without impact to customer deliveries.
“We have dedicated employees who are highly motivated and always rise to the challenges placed in front of them. Upon learning that the products they were making were to be used for medical devices, it gave them extra motivation and determination to succeed at their jobs. It also gave them the satisfaction of contributing a meaningful product to society.” Ryan Karns, Manufacturing Manager, North Campus.
With the material flying off the line, the shipping and receiving teams were adjusting pickup locations by the choice of carriers to ensure they were loading up quickly and getting orders to their destinations.
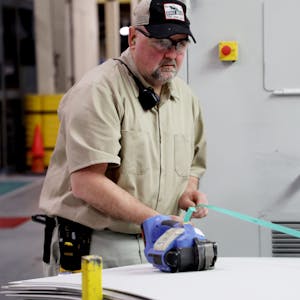
Neil Ryder securing customer orders for shipping.
Last, but not least, our Business Development, Customer Collaboration, Finance, Quality, appLab™, designLab®, and Marketing teams kept the business side moving. From helping customers convert to KYDEX® thermoplastics when other suppliers could not meet critical ship dates, to paying suppliers on time or early to launching new products to support customer needs, the focus was always on you, our valued customers.
When asked about the team’s performance, Nik Taritas, Vice President of Business Development shared “This is an amazing accomplishment based on the market volatility that we have seen over the last 2 years. As the majority of our customers experienced devastating delivery disruptions from other suppliers, we remained constant in on-time delivery. This allowed our customers to keep their people working and maintain their shipping schedules for critical customers. Well done!”
Join us in celebrating our extraordinary people, who during extraordinary times, overcame the challenge of surviving to enter a new state of thriving.